実務で役立つ!SOLIDWORKS測定&センサ活用ガイド エラー削減と品質向上
1. はじめに:SOLIDWORKS測定&センサの可能性
製品設計において、わずかな寸法のズレや設計ミスが、重大なエラーにつながり、製造コストや納期に大きな影響を与えることがあります。特に3D CADソフトウェアとして広く使われているSOLIDWORKSには、こうしたエラーを未然に防ぎ、設計品質を向上させるための強力なツールが用意されています。
その中でも「測定ツール」と「センサ機能」は、設計段階での確認や自動監視を通じて、エラー削減と品質保証に貢献します。たとえば、測定ツールを使えば、部品同士の干渉を検出し、設計段階でクリアランスを確認できます。また、公差解析により指定した寸法が許容範囲内に収まっているかを即座に把握でき、質量特性の機能を使うことで、製品全体の重量や重心を簡単に測定し、強度やバランスの最適化も可能です。
一方、センサ機能を活用すれば、設計中に指定条件から外れた変更が自動的に検出され、即座に警告を受け取ることができます。これにより、手戻りのリスクを最小限に抑え、品質管理が確実に行えます。たとえば、寸法や重量が規定値を超えた場合、あるいは部品が互いに干渉した場合に即座に通知を受けることで、早期に修正が可能です。若手エンジニアであっても、この機能を活用することでベテランエンジニアと同等の品質管理が実現できます。
本記事では、この「測定ツール」と「センサ機能」を効果的に活用し、設計品質を確保しながら効率を高める方法を解説します。まずは測定ツールの基本操作から、次にセンサ機能の設定方法、そして実務での応用例を順に紹介し、最終的にはこれらの機能を組み合わせた高度な活用方法も取り上げます。
読み進めることで、SOLIDWORKSを活用した設計の効率向上と品質確保の具体的な手法を学べます。まずは基本の測定機能から確認していきましょう。
2. 基本の測定機能を理解する
引用:SOLIDWORKSヘルプ:https://help.solidworks.com/2025/japanese/SolidWorks/sldworks/t_measuring_angle_rotation_coordsys.htm
SOLIDWORKSは、単なる3Dモデリングツールに留まらず、設計精度を確保し、品質を向上させるための多彩な解析ツールを備えています。その中でも「測定機能」は、設計の各段階で寸法や角度、クリアランスを確認し、エラーを未然に防ぐための重要なツールです。
この測定機能を使えば、部品間の隙間や角度を正確に把握し、設計仕様が適切に守られているかを瞬時に確認できます。たとえば、組み立てられた部品同士が接触しないか、指定したクリアランスが確保されているか、寸法が設計図通りであるかを、リアルタイムに測定できます。これにより、製造プロセスの後工程で発生しうるトラブルを未然に防止し、設計の信頼性を高めることが可能です。
3D CADならではの大きな利点として、設計段階でデジタルデータをもとに正確な寸法を測定できるため、手作業による測定の誤差やチェック漏れを排除できます。また、部品単体だけでなく、アセンブリ全体の計測も可能であり、組み立て時の干渉チェックや、全体の重量バランス確認にも役立ちます。
ここでは、まず基本的な測定ツールの操作方法を理解し、その後、実務での活用方法についても詳しく解説します。SOLIDWORKSの測定機能を正しく使いこなすことが、設計品質を大きく向上させる第一歩です。
2.1. 測定ツールの基本操作
SOLIDWORKSの測定ツールは、上部メニューの「評価」タブから「測定」を選択することで起動できます。また、ショートカットキーをカスタマイズすることで、より迅速に呼び出すことも可能です。測定ツールを起動すると、画面上でエッジやフェース、頂点などをクリックするだけで、指定した要素間の距離や角度、半径などの情報がリアルタイムで表示されます。
たとえば、アセンブリ内で複数の部品を選択すれば、部品間の中心距離、最近接点までの間隔、さらには角度や直線間の距離も即座に測定可能です。これにより、組立時に部品が互いに干渉しないことを確認し、設計ミスを防ぐことができます。また、個別部品の質量特性を確認することもでき、部品やアセンブリ全体の重量や重心を把握できます。
測定ツールでは、単位設定も柔軟に変更可能です。ミリメートル、センチメートル、インチなど、プロジェクトやチームの標準に合わせた単位で計測できるため、グローバルチームとの情報共有もスムーズです。さらに、測定結果は保存することも可能で、記録画面に残したり、CSV形式でエクスポートして品質管理資料として活用できます。
操作に慣れるためには、小型のサンプルモデルで複数の測定を試すと効果的です。エンジニア同士で測定結果を共有し、どのように公差解析や比較ツールを併用できるかを検討することで、測定の基本操作だけでなく、より高度な使い方にもスムーズに移行できます。
2.2. 測定機能の活用事例
測定機能は実務で幅広く活用でき、設計品質の向上に直接寄与します。以下では、代表的な三つの事例を紹介します。
事例1:稼働部品の設計ミス防止
モーターシャフトとギアの隙間を測定し、動作中に干渉が発生しないことを確認します。たとえば、シャフトの回転に合わせてギアがスムーズに動くか、設計段階でクリアランスを確保できているかを測定することで、後の組立工程で干渉や過剰な摩耗が発生するリスクを低減できます。
事例2:質量特性を活用した軽量化
自動車部品や航空機部品など、軽量化が求められる製品では、質量特性を測定し、重量超過のリスクを早期に検知できます。たとえば、製品全体の重量が指定された値を超えていないか、重心位置が設計仕様に合致しているかを確認し、材料の削減や構造の見直しに活用できます。これにより、安全性を確保しつつ、材料コストを削減することが可能です。
事例3:比較ツールとの連携による設計検証
バージョン変更後の設計を、前バージョンと比較して測定することができます。たとえば、変更前後で寸法が正しく変更されているか、指定した厚みが保たれているか、公差範囲を超えていないかを簡単に確認できます。これにより、複数の設計者が関与するプロジェクトでも、変更内容を確実に検証し、手戻りを防ぐことが可能です。
測定ツールは、設計の正確性を高め、エラーを未然に防ぐための強力なツールです。これらの事例からも分かるように、測定は単なる数値の確認に留まらず、設計の安定性と品質を確保するための基盤となります。
次章では、もう一つの強力なツールである「センサ機能」による設計監視方法を解説します。
3. センサで設計を「スマート」に監視する
引用:SOLIDWORKSヘルプ:https://help.solidworks.com/2025/japanese/SolidWorks/sldworks/c_Sensors_OH.htm
測定ツールによる手動チェックは、設計品質を高めるために非常に効果的です。しかし、設計が進む中で、すべての要素を常に目視で確認することは現実的ではありません。特に複雑な設計や部品数が多いプロジェクトでは、見逃しが発生しやすく、エラーの発見が遅れてしまうリスクがあります。こうした状況で強力な助けとなるのが、SOLIDWORKSの「センサ機能」です。
センサは、指定した条件を自動的に監視し、設定値を超えた場合に警告を表示する仕組みです。たとえば、部品の重量が500gを超えたとき、寸法が指定範囲を外れたとき、または部品同士が干渉したときなど、リアルタイムでアラートを受け取ることができます。これにより、設計中のエラーを見逃さず、修正が必要なタイミングをすぐに把握できます。
このセンサ機能は、特に以下のような状況で大きな効果を発揮します。
- 設計基準が厳格で、寸法や質量が厳密に管理されているプロジェクト
- 製品が複数のエンジニアによって設計されている場合
- 頻繁なデザイン変更が発生し、品質管理が複雑化している場合
センサは一度設定すれば、設計が変更されるたびに自動で監視を続けます。これにより、エンジニアは手動チェックにかける時間を削減し、設計のミスを未然に防ぐことができます。次に、このセンサ機能の基本的な仕組みと、実務での活用方法について詳しく見ていきましょう。
3.1. センサの基本概念
SOLIDWORKSのセンサは、寸法、質量、体積、干渉、さらにはシミュレーション結果まで、多様な要素を監視することができます。指定したパラメータに基づき、条件を満たさなくなった場合、リアルタイムで警告を表示します。
たとえば、寸法センサを設定しておくことで、指定したクリアランスや寸法範囲を超えた場合に警告を発します。これは、設計段階での公差管理を強化し、意図しない形状変更やサイズオーバーを防止する手段として非常に有効です。また、質量センサは製品の重量が指定範囲を超えた場合にアラートを表示し、材料の過剰使用や重量バランスの問題を早期に発見できます。
干渉センサは、アセンブリ内で部品同士が重なったり、接触したりした場合に通知します。これにより、動的なシミュレーション中に干渉が発生するリスクを最小限に抑えられます。たとえば、可動部品が稼働中に他の部品と衝突しないかを確認できるため、安全性が求められる製品の設計には欠かせません。
シミュレーションセンサも強力なツールです。このセンサは「SOLIDWORKS Simulation」での応力解析結果を監視し、指定した条件を超えた場合に警告を出します。たとえば、構造部材にかかる応力が安全基準を超えたときや、変形量が許容範囲を超えたときにアラートを表示します。これにより、設計段階で強度不足を早期に発見できます。
ただし、このシミュレーションセンサは 「SOLIDWORKS Simulation」の応力解析に限定されます。Motion解析(動作シミュレーション)やCosting解析(コスト解析)はセンサ機能で監視できません。これらは、手動で確認するか、解析結果を記録して品質管理を行います。
これらのセンサは、FeatureManager デザインツリーから簡単に設定できます。センサを追加するには、右クリックして「センサ追加」を選択し、監視したいパラメータとそのしきい値を指定するだけです。複数のセンサを同時に設定することで、総合的な設計監視を行うことも可能です。
3.2. 実務で役立つセンサ活用法
センサは設計品質を自動的に確保できるツールですが、その効果を最大化するためには、実務に即した設定が重要です。以下では、代表的なセンサ活用例を紹介します。
1. 寸法管理センサで設計ミス防止
たとえば、締結部品の穴径が規定範囲を外れた場合に警告を出すよう設定できます。こうすることで、部品変更時や設計修正時に誤ったサイズが設定されるリスクを回避できます。また、公差を指定しておけば、設計段階で指定寸法からのズレを即座に検知できます。
2. 干渉検出センサによる組立確認
アセンブリ内で部品が重なると、干渉センサが警告を発します。特に可動部品や複数のパーツが密集する設計では、干渉センサが効果的です。たとえば、ギアやモーターの回転部分で他の部品と接触しないかを常時監視できます。
3. 質量特性センサで製品重量を管理
質量特性センサを使えば、製品重量が設定された上限を超えた場合に通知を受け取れます。これにより、軽量化が求められる製品や、重量制限が厳しい製品でも、設計時点で品質を確保できます。たとえば、自動車部品の重量を500g以下に抑えたい場合、その範囲を超えた瞬間に警告を出すことで、材料の無駄使いを防げます。
4. シミュレーションセンサで構造の強度を監視
応力解析の結果を監視し、指定した応力範囲を超えた場合に警告を発することも可能です。たとえば、航空機の翼部や自動車のシャーシなど、強度が重要な構造部品で効果を発揮します。設計変更時に強度不足を即座に検出できるため、製品安全性が確保されます。
センサ機能は、エンジニアに代わって設計を監視し、品質を守る「自動チェックシステム」として機能します。設定次第で監視項目を柔軟に変更でき、設計の信頼性を大幅に向上させることが可能です。
次章では、このセンサ機能と測定ツールを組み合わせた効率的なワークフローを解説します。これにより、設計品質を確保しながら作業効率を大幅に向上させる方法を確認しましょう。
4. 設計プロセスへの統合:ワークフローの改善
SOLIDWORKSの測定ツールとセンサ機能は、個々に使うだけでも設計品質を向上させる強力なツールです。しかし、その真価を発揮するのは、これらを設計プロセス全体に組み込み、チーム全体で統一したワークフローとして運用する場合です。測定とセンサを効果的に組み合わせることで、設計品質を確保しつつ、作業効率も大幅に向上させることができます。
測定ツールは、設計者が手動で寸法やクリアランス、質量を確認し、仕様通りに設計が進んでいるかを確認するためのツールです。一方、センサ機能は、設定した条件を常時自動監視し、設計基準から逸脱した場合に警告を発する自動チェックシステムです。これらを組み合わせることで、設計の各段階で品質を確認し、問題があれば即座に修正できます。
たとえば、新規設計を開始する際、まず測定ツールで基本寸法やクリアランスを確認し、製品の基本構造を正確に定義します。その後、センサを設定し、設計が進む中で指定した基準から外れないことを自動的に確認できます。これにより、手動確認の抜け漏れを防ぎつつ、設計が常に正しい基準を維持することが可能です。
さらに、このワークフローをチーム全体で共有すれば、複数のエンジニアが関与するプロジェクトでも、設計品質を統一して確保できます。特に、PDM(Product Data Management)システムを活用すれば、センサ設定や測定結果をプロジェクトテンプレートとして保存し、チーム全員が同じ設定で設計確認を行えます。
4.1. 設計初期段階からのセンサ活用
設計プロセスで最も重要なのは、設計初期の段階から測定とセンサを導入し、エラーを早期に発見できる体制を構築することです。設計初期は、基本的な構造や寸法が決まり、全体の仕様が確定していく段階です。この時点で基準をしっかり設定しておくことが、後の手戻りを防ぐ鍵となります。
たとえば、製品の寸法やクリアランスを測定ツールで確認し、センサで指定した寸法範囲を設定しておくと、設計が進む中でその範囲を超えることがあれば即座に警告を受け取れます。これにより、設計の初期段階から品質を確保でき、後から修正が必要になるリスクを最小限に抑えられます。
また、質量特性センサを設定しておけば、製品重量が設計基準を超えることなく進行できます。たとえば、自動車部品で500g以下に抑えたい場合、質量特性センサを設定し、設計中に重量超過があればアラートが表示されます。これにより、材料コストの抑制と製品性能の両立を実現できます。
このように、設計初期から測定とセンサを組み込むことで、製品仕様が明確になり、チーム内で統一された品質基準を共有できます。特に若手エンジニアにとっては、センサ設定が「品質の目安」となり、ベテランの指導を受けることなく高品質な設計が可能です。
4.2. チーム設計での活用法
複数のエンジニアが関与するチーム設計では、作業内容が複雑化し、個々の判断ミスが製品品質に影響を与えるリスクが高まります。こうした環境でも、SOLIDWORKSの測定ツールとセンサ機能をチーム全体で統一的に運用すれば、品質管理を徹底できます。
まず、プロジェクトテンプレートを設定し、すべての設計に共通の測定基準とセンサ設定を含めます。たとえば、寸法センサで製品の最小クリアランスを1mmに設定し、質量特性センサで重量を500g以下に制限するなど、チーム標準を明確に定義できます。こうすることで、各エンジニアが個別に設定する手間を省き、品質基準が一貫します。
PDMシステムを活用すれば、これらのテンプレートをプロジェクトごとに保存し、新たなプロジェクトを開始するたびに自動的に適用できます。さらに、設計中にセンサのアラートが発生した場合、その履歴をPDMで記録し、設計レビューで確認できます。これにより、エラー発生時の原因特定も迅速に行えます。
また、チーム設計では定期的な設計レビューが重要です。センサのアラート履歴を確認し、どのタイミングで問題が発生したか、どのように修正されたかをチーム全員で共有できます。これにより、エラー発生パターンの把握や、設計ミス防止のための改善策をチーム全体で検討できます。
特に新入社員や若手エンジニアも、先輩が設定したセンサ設定を参考にしながら設計を進められるため、品質を確保しながら学びを深めることができます。センサ設定が「品質基準」として機能し、設計ルールが自然と身につくため、チーム全体のスキルアップにもつながります。
4.3. 測定&センサを活用した品質管理のチェックリスト
設計品質を確保しつつ効率的に設計を進めるためには、測定とセンサを組み合わせたチェックリストを導入することが効果的です。以下は、設計プロセスにおける確認事項の例です。
設計開始前
- プロジェクトテンプレートで基準設定(寸法センサ、質量センサなど)
- チーム全員でセンサ設定の確認
- 測定ツールで基準寸法とクリアランスを確認
設計中
- 部品間のクリアランスを測定し、干渉がないことを確認
- 質量特性センサで重量超過を監視
- 干渉センサでアセンブリ全体の衝突を自動監視
設計完了後
- センサアラート履歴を確認し、エラーがないことを確認
- 測定結果をCSVでエクスポートし、品質管理資料として保存
- チームレビューで設計品質を確認し、問題があれば修正
このチェックリストをチームで共有し、プロジェクトごとに確認を徹底することで、設計品質を安定的に維持できます。また、エラー発生率が高いセンサや測定項目は、次回以降のテンプレートに改善を反映し、継続的な品質向上を図ることが可能です。
次章では、これらの測定ツールとセンサ機能をさらに応用し、設計の効率を劇的に向上させる高度な活用テクニックを紹介します。
5. 高度な活用テクニック
SOLIDWORKSの測定ツールとセンサ機能は、基本的な使用だけでも設計品質を向上させる効果がありますが、それだけではありません。これらをさらに応用し、カスタマイズすることで、設計業務を大幅に効率化し、自動化することが可能です。特に、大規模なプロジェクトや複数の設計者が関与するチーム設計では、これらの高度な活用テクニックが大きな威力を発揮します。
この章では、測定ツールとセンサ機能をより高度に活用するためのテクニックを紹介します。具体的には、マクロによる自動化、複数センサの連携による総合監視、さらにセンサデータの収集と分析により、設計品質をさらに向上させる方法を解説します。これにより、単なる設計確認から一歩進んだ「インテリジェントな設計管理」を実現できます。
5.1. マクロとセンサの組み合わせ
マクロを活用すれば、測定ツールやセンサ機能を自動化し、繰り返し行う手作業を削減できます。SOLIDWORKSは、Visual Basic for Applications(VBA)を使用してマクロを作成でき、測定結果の自動記録やセンサアラートの自動通知など、さまざまな操作を自動化可能です。
自動化の実例:測定結果の記録
たとえば、複数の部品のクリアランスを測定し、その結果を自動でCSVファイルに保存するマクロを作成できます。これにより、手動で測定結果を記録する手間がなくなり、品質管理資料を迅速に作成できます。また、設計変更後に再測定しても、マクロを実行するだけで最新の測定結果を取得できます。
自動通知:センサアラートのリアルタイム共有
センサによってエラーが検出された場合、マクロを使ってその通知を自動でメール送信することも可能です。たとえば、センサで重量が500gを超えた場合、担当エンジニアにメールで通知され、すぐに設計修正が可能です。これにより、問題の見逃しを防ぎ、修正対応を迅速化できます。
マクロ作成の基本手順
- SOLIDWORKSでVBAエディタを起動
- 測定ツールやセンサに関連するコマンドを記述
- トリガー条件(センサアラートや測定開始時)を指定
- 出力形式(CSV、メール通知など)を設定し保存
このように、マクロとセンサを組み合わせることで、設計品質の監視が完全に自動化され、エラー発見から修正までのスピードが劇的に向上します。
5.2. 複数センサの連携による高度な監視
SOLIDWORKSのセンサ機能は、単体でも強力ですが、複数のセンサを組み合わせて連携させることで、より複雑な設計監視を実現できます。これは、特に高精度が求められる製品設計や、複数の要素が連動する構造設計で効果を発揮します。
複数センサ連携の実例
たとえば、航空機部品の設計では以下のような監視が必要です:
- 寸法センサで各部材の厚みを監視し、安全範囲を超えないことを確認
- 質量センサで製品全体の重量が指定値を超えないことを監視
- シミュレーションセンサで応力解析結果が安全基準内であることを確認
これらのセンサを組み合わせることで、設計が常に安全で軽量かつ強度を確保できているかをリアルタイムで監視できます。たとえば、部材の厚みを変更すると、即座に質量センサとシミュレーションセンサも再確認され、設計変更の影響を即時に把握できます。
連携設定の手順
- 各センサをFeatureManagerから追加し、それぞれの監視条件を設定
- 複数のセンサを同一のアセンブリまたは部品に適用
- 設計変更時に自動的に全センサが再評価されるよう設定
- センサアラートをPDMシステムで記録し、履歴管理を実施
このように、複数センサを連携させることで、設計監視の精度が大幅に向上し、複雑な設計でも高品質を維持できます。
5.3. データ収集と分析
センサ機能を活用して設計品質を監視するだけでなく、その監視結果をデータとして収集・分析することも重要です。これにより、設計品質の傾向を把握し、次回以降のプロジェクトで同様のエラーを未然に防ぐことができます。
センサデータの収集
各センサのアラート履歴は、SOLIDWORKSの履歴管理機能やPDMシステムで自動的に記録できます。たとえば、設計中に発生した重量オーバーの回数や、干渉検出の発生場所などを記録し、設計終了後にその履歴を確認できます。
分析の活用例
- どの部品でエラーが多発しているかを特定
- 特定のセンサ(重量、干渉、寸法)でのエラー発生率を可視化
- エラー発生のタイミング(設計初期、中盤、最終確認)を把握し、改善点を特定
データ分析からのフィードバック
たとえば、複数のプロジェクトで重量オーバーのアラートが頻発している場合、設計段階での材料選定や形状最適化に問題がある可能性があります。この場合、次回プロジェクトのテンプレートにあらかじめ厳しめの質量センサを設定し、エラー削減を図れます。
また、エラーの発生が特定の部品に集中している場合は、その部品の設計基準や公差設定を見直すことで、品質の安定化を図ることが可能です。データを分析し、そこから得られた知見をプロジェクトにフィードバックすることで、継続的な品質向上が期待できます。
5.4. 自動化とデータ活用によるインテリジェントな設計管理
この章で紹介したテクニックを組み合わせれば、SOLIDWORKSを単なる設計ツールから、設計品質を自動監視し、データに基づいて改善を進める「インテリジェントな設計管理ツール」として活用できます。
- マクロで測定&センサ機能を自動化し、設計チェックを効率化
- 複数センサを連携させ、複雑な製品でも一貫した品質監視を実現
- センサデータを収集し、エラー傾向を分析して次回プロジェクトに反映
これにより、設計プロセスは手作業から自動化・データ駆動型へと進化し、チーム全体の設計品質が飛躍的に向上します。次章では、これらのテクニックを実務に応用した事例を具体的に紹介します。
6. センサと測定機能の事例別応用シナリオ
SOLIDWORKSの測定ツールとセンサ機能は、特定の業界や用途に限定されることなく、さまざまな分野で設計品質の向上とエラー削減に役立ちます。ここでは、代表的な三つの業界(航空宇宙、医療機器、自動車部品)を例に、それぞれの分野でどのようにこれらの機能が活用できるのか、想定シナリオに沿って紹介します。
6.1. 航空宇宙分野での活用シナリオ
航空宇宙産業では、製品の軽量化と高い構造強度が求められます。部品の寸法精度や重量管理は、製品の安全性やパフォーマンスに直結するため、SOLIDWORKSの測定ツールとセンサ機能は欠かせません。
測定ツールでの活用:寸法と重量の確認
航空機の翼部品やエンジン構造では、寸法精度が重要です。測定ツールを使えば、リブの厚みや桁(けた)の長さをミリメートル単位で正確に測定できます。また、質量特性を測定し、部品ごとの重量を確認することで、総重量が設計仕様を超えないように管理できます。たとえば、機体全体の重心位置を測定し、バランスが設計仕様に合致しているかを確認できます。
センサ機能での活用:リアルタイム監視
航空宇宙分野では、設計段階から強度と安全性を確認する必要があります。センサ機能を活用し、以下のような自動監視が可能です:
- 寸法センサ:翼部のリブ厚みが設定範囲を外れた場合に警告
- 質量センサ:部品重量が指定範囲を超えた場合にアラート
- 干渉センサ:アセンブリ内で部品同士が干渉した場合に通知
- シミュレーションセンサ:応力解析で指定応力を超えた場合に警告
たとえば、設計変更によりリブの厚みを削った際、即座に重量センサと応力センサが再評価され、軽量化と強度維持のバランスをリアルタイムで確認できます。これにより、航空機の安全性を確保しつつ、設計効率も向上します。
6.2. 医療機器分野での活用シナリオ
医療機器は人体に直接関わるため、高い安全性と精度が求められます。寸法のわずかなずれが、患者の健康に大きな影響を及ぼす可能性があるため、厳密な品質管理が必要です。SOLIDWORKSの測定ツールとセンサ機能は、こうした品質基準を維持するために強力なサポートを提供します。
測定ツールでの活用:高精度の寸法管理
インプラントや外科用器具など、ミリメートル未満の寸法精度が必要な部品には、測定ツールで寸法を確認し、公差範囲内に収まっているかをチェックできます。たとえば、人工関節のパーツは、相互に正確に組み合わさる必要があります。測定ツールで各パーツの寸法を確認し、設計図通りの精度で製造されているかを確認できます。
センサ機能での活用:安全基準の監視
医療機器では、使用中の安全性も確保する必要があります。センサを設定し、以下の監視が可能です:
- 寸法センサ:部品の直径や長さが規定範囲を超えた場合に警告
- 干渉センサ:アセンブリ内で部品が重なり、正しく装着できない場合に通知
- 質量センサ:材料が指定重量を超えた場合にアラート
- シミュレーションセンサ:応力や変形量が安全基準を超えた場合に警告
たとえば、インプラントの強度解析で、指定した応力範囲を超えた場合にアラートを出し、材料強度を再確認できます。これにより、製品の安全性を高め、医療現場でのトラブルを未然に防ぐことができます。
6.3. 自動車部品分野での活用シナリオ
自動車産業では、部品の精度と耐久性が重要で、さらに軽量化やコスト削減も求められます。SOLIDWORKSの測定ツールとセンサ機能は、これらの要件を満たすための品質管理に大きく貢献します。
測定ツールでの活用:構造とクリアランスの確認
シャーシ部品やエンジン構造で、部品間の隙間を測定し、適切なクリアランスが確保されているかを確認できます。たとえば、エンジン内のピストンとシリンダーの隙間を測定し、動作時に摩擦が発生しないよう管理できます。また、部品の質量特性を測定し、燃費や走行性能に影響を与える重量管理も可能です。
センサ機能での活用:自動監視とエラー防止
自動車部品は、複数のエンジニアが設計し、頻繁にデザイン変更が発生するため、センサによる自動監視が特に効果的です:
- 干渉センサ:部品が動作中に干渉する場合に警告
- 質量センサ:エンジン部品の重量が規定を超えた場合に通知
- 寸法センサ:部品の穴径やネジサイズが指定値を超えた場合にアラート
- シミュレーションセンサ:衝突シミュレーションで変形量が規定を超えた場合に警告
たとえば、車両のサスペンション部品では、干渉センサを設定し、スプリングの動作中に他の部品と衝突しないことを確認できます。また、車体重量を管理するために質量センサを設定し、燃費向上と走行性能のバランスを保つことが可能です。
6.4. 業界を超えた応用力
これら三つの業界に共通するポイントは、「測定ツールで設計を確認し、センサで自動監視する」という一貫した品質管理の流れです。航空宇宙では安全性と軽量化、医療機器では高精度と安全性、自動車部品では耐久性と効率性が求められますが、いずれもSOLIDWORKSの測定&センサ機能でカバー可能です。
さらに、これらの応用例を自社の設計プロジェクトに合わせてカスタマイズすれば、どの分野でも品質を高めつつ、設計効率を向上させることが可能です。特にセンサ設定は、設計基準に合わせて自由にカスタマイズでき、エラー発生を未然に防ぐ「自動チェックシステム」として機能します。
次章では、これまで紹介してきた測定ツールとセンサ機能を総合的に活用し、設計品質と作業効率を最大化する方法をまとめます。
7. まとめ:測定機能とセンサ活用の実務における価値
SOLIDWORKSの測定ツールとセンサ機能は、製品設計における品質向上とエラー削減を実現する強力なツールです。測定ツールは、寸法や角度、質量を正確に確認し、設計図通りの精度を確保できます。これにより、設計段階でのミスを早期に発見し、組み立てや製造時のトラブルを未然に防げます。
一方、センサ機能は指定条件をリアルタイムで監視し、基準から外れた場合に自動で警告を発します。これにより、設計中にエラーを検出し、修正が必要な箇所を即座に特定できます。たとえば、部品が干渉したり、重量が指定範囲を超えた場合にも即座に対応が可能です。
これらのツールは、単独で使用するだけでなく、設計プロセス全体に統合することで、さらに効果を発揮します。設計開始時に測定ツールで基本を確認し、進行中はセンサで自動監視を行うことで、品質確認が継続的に行えます。さらに、チーム全体で共有すれば、複数のエンジニアが関わるプロジェクトでも品質基準を統一できます。
最終的には、マクロや複数センサの連携で自動化を進め、インテリジェントな設計管理を実現できます。エラー検出から修正までをスムーズにし、設計品質を安定させながら効率も向上できます。SOLIDWORKSの測定ツールとセンサ機能を活用し、エラー削減と品質向上を両立させましょう。
建築・土木業向け BIM/CIMの導入方法から活用までがトータルで理解できる ホワイトペーパー配布中!
❶BIM/CIMの概要と重要性
❷BIM/CIM導入までの流れ
❸BIM/CIM導入でよくある失敗と課題
❹BIM活用を進めるためのポイント
についてまとめたホワイトペーパーを配布中
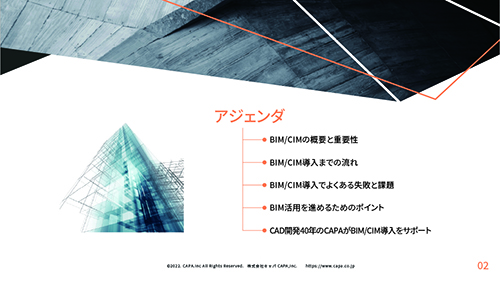
参考情報
・SOLIDWORKSヘルプ:測定ツール(Measure Tool)
https://help.solidworks.com/2025/japanese/SolidWorks/sldworks/HIDD_MEASURE.htm
・SOLIDWORKSヘルプ:センサー(Sensors)
https://help.solidworks.com/2025/japanese/SolidWorks/sldworks/c_Sensors_OH.htm