3D CAD×熱解析:基礎原理とシミュレーション手法の徹底解説
はじめに
近年、製品開発の高度化と短納期化が進む中、3D CADで作成したモデルを用いた熱解析は、設計段階の早期に潜在的な問題を洗い出すうえで非常に有効な手段になっています。従来は試作や実機評価に多くの時間とコストがかかりましたが、数値解析を駆使することで、温度分布や熱の流れを事前に把握し、確度の高い設計計画を立てることが可能になりました。
特に自動車や航空宇宙、電子機器など幅広い業界で、熱管理の重要性が増しており、例えば高発熱部品の配置や冷却ファンの設計を検討する際、3D CADから得られる正確なジオメトリ情報をもとに熱伝導や対流、放射といった複数の熱伝達要素を考慮したシミュレーションを行うと、最適なレイアウトや部品選定が見えてきます。また、このアプローチは単に熱設計にとどまらず、応力解析との連携を図ることによって、温度変化が部品に与える影響を総合的に評価することも可能です。
こうした複合的な解析を実践すれば、不具合発生リスクの減少や製品リードタイムの短縮につながり、設計プロセス全体の質と効率を高められます。さらに、最新の解析ソフトウェアではAI解析やマルチフィジックス解析の導入が進み、シミュレーション自動化やクラウド計算により大規模なモデルを高速に扱える環境も整ってきています。
本記事では、3D CADと熱解析を連携させる際の基礎理論やシミュレーション手法を体系的に紹介し、幅広い読者の顕在ニーズである「効率的な解析手法の習得」をサポートすると共に、潜在ニーズである「高度な技術との連携や設計プロセスの抜本的な時間短縮」にも役立つ視点を提供します。これを通じて、先端技術を効果的に活用しながら製品開発を進めるための具体的なヒントを得ていただければ幸いです。
3D CADと熱解析の基本概念
3D CADと熱解析を効果的に組み合わせるためには、まず両者の基本的な役割や考え方を理解することが大切です。
3D CADは製品開発においてジオメトリ最適化や設計変更を容易に行うための基盤技術であり、製品形状をデジタルデータ化して管理することができます。
一方、熱解析は数値解析技術の一端として、有限要素法や有限体積法、そして境界要素法など多様な手法を駆使し、熱伝導や対流、放射といった現象を数式モデルに落とし込み、コンピュータを用いてシミュレーションする工程を指します。
これらのシミュレーション技法を適切に活用すれば、温度分布がどのように広がるかを定量的に可視化し、設計改善の方向を客観的に判断できます。特に、3D CAD上で作成した高精度のモデルを解析ソフトウェアに読み込むことで、複雑な形状のメッシュ生成を効率的に行い、より実態に近い熱挙動のシミュレーションが可能になるのです。たとえば、ANSYSやCOMSOL、SimScaleといった解析ソフトは3D CADとのデータリンクを強化しており、ユーザーはGUIを通じて簡単に境界条件設定や初期条件の入力ができるようになっています。
また、このような数値解析技術を導入することは、開発コストや時間を削減するだけでなく、製品の信頼性と長期安定性を高めることも挙げられます。現代においては、小型化・高機能化が進む中での熱管理が製品開発のボトルネックとなるケースも多く、従来の経験則や試行錯誤だけでは対応が難しい局面が増えています。そのため、3D CADと熱解析を組み合わせて科学的にアプローチする意義はますます高まっているのです。
3D CADの役割
3D CADは製品開発の初期段階でアイデアを形にし、詳細設計や寸法検討を進める中核ツールです。特に複雑な部品形状や内部構造を表現するとき、3次元的な可視化は設計者のイメージを正確に反映できます。さらに、近年のソフトウェアではパラメトリックモデリングやアセンブリ機能が充実し、多数の部品を統合した全体最適な設計を行いやすくなっています。
例えば部品を追加・削除したり寸法を変更しても、関連する寸法や拘束条件が自動的に更新されるため、試行錯誤を繰り返す設計プロセスにおいて大きな効率化が期待できます。3D CADの基本操作としては、スケッチ機能を用いて断面図を描き、押し出しや回転、スイープなどの操作によって三次元形状を生成する方法が挙げられます。また、GUI上で組み立て環境を用いれば、複数パーツを確実に配置し、干渉チェックや質量計算などの動的な評価も可能です。
これらのプロセスを踏む中で、設計者は実際の製品をイメージしながら、必要に応じてジオメトリ最適化を繰り返します。最終的に得られたデジタルモデルは、熱解析のみならず応力解析や振動解析といったマルチフィジックス解析の出発点としても活用されます。特に塗装や表面処理を想定した場合は、その塗布厚みまで考慮した正確なモデル化が行われることが重要です。これにより製品の熱伝導特性や表面放射特性をより忠実に再現できるので、後述する熱解析にも高い精度がもたらされます。
こうした3D CADでのモデリングと解析の連携は、エンジニアにとって日常的な作業フローの大きな変革をもたらすものであり、高度化する製品の設計品質を支える基盤になっているのです。
熱解析の基本原理
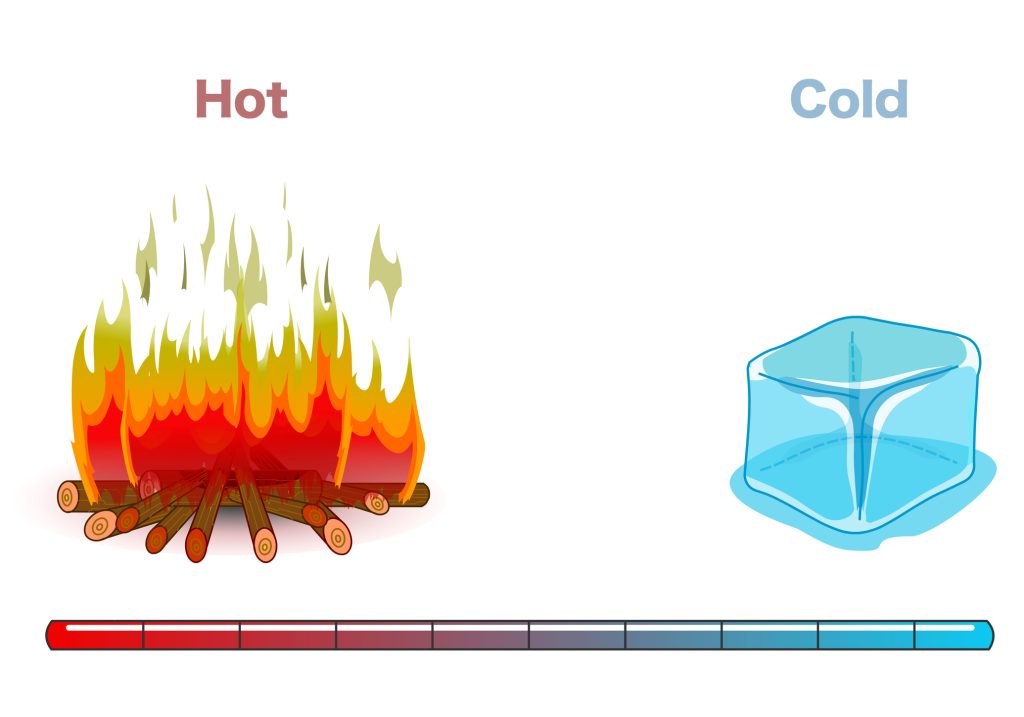
熱解析の基本原理を把握するうえでは、まず熱伝導、対流、放射の3種類の熱移動現象を深く理解する必要があります。これらは設計者がシミュレーションを行う際に必ず考慮すべき要素であり、製品全体の熱的挙動に大きな影響を与えます。特に対流の取り扱いが難しく、解析ソフトウェアによっては流体領域のメッシュ生成やタービュランスモデルの選定が大きなポイントとなります。
また、数値解析手法として代表的な有限要素法は物体を多数の要素に分割することで解析を行うのに対し、有限体積法は流体解析によく使用され、要素体積ごとにエネルギーバランスを求める手法です。境界要素法は表面だけを要素化して現象を解析する方法で、放射のモデリングに使われることもあります。このように解析対象や設計目的、ソフトウェアの特徴に合わせて最適なアプローチを使い分けることが望ましいです。
さらに、正確な熱解析を行うためには、境界条件の設定とパラメータ設定も重要になります。たとえば外気温や放熱面の温度、流体の流れを制御するファンの風速や流量など、物理的実態に即した値を入力しないと、いくらモデルが精密でも精度の高い結果は得られません。こうした手順を踏むことにより、実機さながらのシミュレーション自動化が進められ、製品開発の効率を大きく向上させられます。
熱伝導、対流、放射
熱伝導は物体内部で温度差があるとき、その差を均一化する方向に進む熱の移動現象です。フーリエの法則に基づき、熱伝導率が高い材料ほど熱が伝わりやすく、放熱設計ではヒートシンクがこの特性を積極的に利用します。
対流は、流体の移動により熱が運ばれる現象で、自然対流と強制対流に大別されます。電子機器ケース内部にファンを取り付けて強制対流を発生させることで、部品の温度上昇を制御するケースは非常に多いです。一方、自然対流は空気や液体が温度差によって生じる浮力で循環するため、設計者の意図で流量を大幅に制御しにくい面があります。
放射は赤外線などの電磁波を介して熱が移動するメカニズムであり、高温部品から放射された熱が周囲の壁や他部品を温める形になります。特に真空環境を想定する宇宙用機器や高出力LEDの冷却設計などでは、放射が熱管理に占める割合がかなり大きくなるため、解析ソフトウェアで適切な放射モデルを組み込むことが欠かせません。3D CADモデル上で材料別の放射率を指定し、メッシュ生成後にシミュレーションを走らせることで、温度分布への放射寄与を定量的に検証できます。
これら3つの熱移動現象はいずれも相互に関連しており、例えば表面温度が上がれば放射熱量も増えるなど、単独で切り離せない性質をもっています。だからこそ、マルチフィジックス解析の視点が重要となり、各要素を同時に扱うことが製品品質を高めるカギといえます。
数値解析手法の概要
数値解析では、製品やシステムに対する熱的な状態を離散化という工程を通じて数式として取り扱います。有限要素法は構造解析で広く利用される手法ですが、熱解析にもよく適用されます。解析領域を小さな要素に分割し、要素ごとに温度や熱流束などを未知数として方程式を立てるので、几何学的に複雑な形状にも対応しやすいメリットがあります。
一方、有限体積法は流体の解析に用いられることが多く、各セルごとにエネルギー保存則を適用することで熱と流体の挙動を同時に扱える利点があります。この方法は対流項の取り扱いが比較的簡明で、乱流モデルなども導入しやすい特徴があります。
境界要素法は主に表面だけを要素に分割してシミュレーションを行うため、モデルサイズを削減できる場合もあります。特に放射熱伝達や大規模空間の取り扱いで有鋭性を発揮することがありますが、ソフトウェアや解析環境によっては設定が難しい面も否めません。
実際の解析手順としては、まず3D CAD上でモデリングを終え、解析ソフトウェアにモデルをインポートして、メッシュ生成を行います。次に、材料特性や境界条件設定を行い、解法アルゴリズムや収束判定基準を選択します。そして初期条件を設定したら、シミュレーションを実行して、結果の可視化で温度分布や熱流束をチェックします。必要に応じてファンの回転数や部品配置を変え、再度シミュレーションを行うというループを繰り返すことで、計算負荷と精度のバランスを取りながら最適な製品設計へと近づけるのです。
パラメータ設定と境界条件の設定
シミュレーションの精度を左右する最も重要なポイントの一つが、パラメータと境界条件の正確な設定です。例えば、材料の熱伝導率や比熱などは温度依存性を持つ場合があり、高温での物性値が大幅に変わることもあります。こうした特性を正確に反映させたい場合は、温度別に物性値が変化するテーブルを入力したり、解析ソフトウェア側で設定可能な非線形モデルを選択することも有効です。
また境界条件に関しては、外気との熱交換があれば対象物の表面上に熱伝達係数を設定し、ファンを使用する場合はその風量や流速、さらには流体中の乱流特性を正しく入力する必要があります。これを怠ると、いくら高精度のメッシュや数値手法を用いても解析結果に乖離が生じる可能性が高くなります。
さらに、初期条件の設定も重要で、たとえば定常解析であっても開始時刻の温度分布は解の収束に影響します。特に過渡解析の場合は開始時点で部品や環境が何℃なのかを厳密に定義しておかないと、結果が大きく変化することがあるのです。
こうした要素を総合的に勘案しながら、トライ&エラーを繰り返しつつモデル化を洗練していく作業が数値解析の醍醐味でもあります。つまり、優れた熱解析は正確なジオメトリ情報があるだけでなく、いかに実環境に即した境界条件や材料特性を設定できるかにかかっています。そのためには試験データの活用や経験豊富なエンジニアとの連携が求められ、社内外のリソースを組み合わせながら最適解を見出していく姿勢が欠かせません。
熱解析シミュレーション手法
ここでは、具体的にどのような手順で熱解析のシミュレーションを進めていくのか、流れを詳しく見ていきます。一般的には、ジオメトリ情報の取り込みからメッシュ生成、境界条件設定や解析ソフトウェア上での数値計算の実行、そして結果の可視化と評価というステップで進められます。特に3D CADデータを活用することで、形状モデリングにおける不整合を減らし、シミュレーション自動化の推進にも繋げることができます。
その一方で、実際の工程では様々なケースがあり、形状が複雑すぎる場合はメッシュ生成が膨大になって計算時間が延びることもあるため、設計者はジオメトリ最適化と解像度とのバランスを検討しながら作業を進める必要があります。また、シミュレーションの種類も定常解析と過渡解析の区分だけでなく、熱応力解析や流体-熱連成解析など、多彩な拡張が可能です。最適なアプローチを選択することで、より正確かつ重要な設計情報を得られるようになります。
ジオメトリとメッシュ作成
まず最初に行うべきは、3D CADで作成したジオメトリのインポートと、その形状をもとにしたメッシュ生成です。ジオメトリは、製品の複雑な形状を忠実に再現しているほど解析精度が向上しますが、一方でメッシュの細分化が極端に増し、膨大な計算リソースを必要とする可能性があります。
そのため、不要な曲面の簡略化やフィレットの無視、対称性の活用といった方法でモデルを簡素化する“ジオメトリ最適化”がよく行われます。そしてメッシュ生成では、要素サイズや要素形状を適切に設定し、重要な領域には細かい要素を割り当てる一方、影響の小さい領域の要素は大きくして計算コストを抑えるように調整します。これは有限要素法にせよ有限体積法にせよ重要な手順であり、メッシュの質が悪いと計算が収束しなかったり、誤差が大きくなったりするリスクが高まります。
最近の解析ソフトウェアは自動メッシャーを備えており、簡単なモデルなら高速かつ一定レベルの品質を確保できることも多いですが、設計要求が厳しく複雑形状となる場合、エンジニアが手動で境界層メッシュや局所細分化を行うことが依然として重要です。実地の製品開発では、ここで時間と手間をかけることで後段の解析速度や精度が大きく向上し、トータルの開発期間を短縮することにつながるケースもあります。
特に流体解析や過渡的な熱応答を重視する場合は、メッシュ生成が結果を左右すると言っても過言ではなく、事前に少量要素のテスト解析を行いながら最適な分割方法を探索するのが一般的な手法です。
シミュレーション実行のステップ
メッシュ生成を終えたら、いよいよシミュレーション設定に入ります。まずは材料特性の入力です。材料固有の熱伝導率、比熱容量、密度などを正確に設定しなければなりません。次いで境界条件設定を行いますが、外気温や自然対流のパラメータがある場合はその値、ファンを設置するなら強制対流の風速や流体密度の入力が必要です。さらに、部品間の接触熱抵抗や熱放射率といった詳細も適宜設定しておくと、結果の精度が格段に向上します。初期条件の設定では、定常解析であっても推奨初期温度を与えることで収束を早めることができますし、過渡解析の場合は具体的な時間ステップの設定やシミュレーション終了までの期間を決めておくことが大切です。
解析ソフトウェアの種類によっては、ソルバーの選択肢も複数あり、陰解法や陽解法、乱流モデルの選定、放射モデルの有無など細かく制御できる場合があります。これらのパラメータを適切に選ぶためには、製品の設計仕様や使用環境の理解が不可欠です。たとえば強い乱流が発生する冷却ファンを伴う電子機器なら、k-εモデルやk-ωモデルといった一般的な乱流モデルを適用するのが通例です。
設定が完了したらシミュレーションを実行し、計算負荷が高い場合はクラウドリソースを活用するのも一手です。最近ではAI解析やシミュレーション自動化を組み合わせて、複数パラメータを自動で最適化するシステムも登場しており、時代の要請に応じて技術革新も進んでいます。こうした一連のステップを着実に踏むことで、信頼できる熱解析結果を得ることが可能になります。
結果のビジュアライズと評価方法
シミュレーションが完了したら、解析結果の可視化を行います。多くの解析ソフトウェアでは、温度分布や熱流束、圧力分布などをカラーコンターやベクトル図形で表示できる機能が用意されています。これによってホットスポットや冷却が不十分な箇所、対流の流路が意図通りかどうかなどを一目で把握できます。
さらに、プローブ機能を使えば特定の箇所の温度や流速を数値でモニタリングし、設計要件を満たしているか詳細にチェックすることが可能です。その後の評価では、解析結果が実験データや既存の設計で得られた性能指標とどの程度合致しているかを比較・検証します。もし差異が大きい場合は、境界条件設定やメッシュの再検討、あるいは材料特性の見直しを行う必要があるでしょう。
さらに、解析結果を基に応力解析を連成させ、温度上昇や急激な温度変化による熱ひずみ・熱応力を評価するケースも多いです。熱応力が大きすぎると部品破損や配線断線などのリスクにつながるため、熱解析から得られた温度分布を構造解析モジュールに引き継ぎ、総合的に製品性能を検討するわけです。
こうした可視化と評価の工程を丁寧に行うことで、製品の安全性・信頼性を高め、不具合を未然に防いで製品開発の成功につなげられます。設計者はこのプロセスを通じて得られる知見を蓄積し、次世代の設計プロセスにフィードバックすることで、組織全体の技術力向上やノウハウの共有にも大きく寄与するのです。
3D CADデータを活用した解析事例
ここでは、3D CADデータを用いて熱解析を行った例を取り上げ、シミュレーション結果がどのように設計改善に役立ったのかを見ていきます。
実際の製品開発現場では、CADモデル上で多種多様な部品構成や配置を試した上で、熱問題が生じやすい領域を早期に発見することが重要となります。製品の小型化や高性能化が進む現代では、熱の課題をクリアできなければ量産段階まで進めなかったり、市場投入後に信頼性クレームが発生するリスクも考えられます。そのため、3D CADモデルを使った事前のシミュレーションは、品質確保と開発スピード向上を同時に達成する手段の一つといえるでしょう。
熱解析ケーススタディ
一例として、電子機器に搭載されるパワーモジュールの熱解析があります。これは高電流を扱う部品であり、発熱が大きいため、従来は大型ヒートシンクを付加して放熱対策をしていました。しかし、製品を小型化するプロジェクトに際し、ヒートシンクの大型化がスペース上難しく三次元的な配置検討が求められたのです。
そこで、3D CADモデル上で部品レイアウトや基板配置、ファン導入位置などを試行しながら、SimScaleを利用して定常解析と過渡解析を実施しました。シミュレーションではまず、メッシュ生成の段階で発熱部品周辺を細密化し、冷却ファンや通気口からのエアフローを考慮に入れることで、どこにホットスポットが集中しやすいかを可視化しました。
その結果、当初の設計では基板の特定コーナー付近に温度が集中しやすいことが判明し、ファン位置を若干ずらすことで冷却効率を大幅に向上できるとわかりました。また、放射の寄与も多いと考えられる高温部については、表面仕上げを反射率の高いコーティングに切り替えることで数℃の温度低減を実現したのです。
このように3D CADデータと熱解析を組み合わせたケーススタディは、経験や試行錯誤だけでは把握しきれない潜在的な熱問題を浮き彫りにし、製品設計の抜本的な改善を可能にします。開発チーム内でシミュレーション結果を共有すると、他のステークホルダーも課題点の理解が深まり、スムーズに仕様変更やコスト検討を進めやすくなるという副次的なメリットも得られました。
シミュレーション結果が設計改善にどう寄与したか
前述のパワーモジュール事例では、従来型の大型ヒートシンクを使わずに、ファンの流路最適化と表面処理変更だけで許容温度内に収めることが可能になりました。これは、物理試作による検証を待たずして早期に最適案を導き出した例といえ、製品開発のスケジュールを大幅に短縮する結果をもたらしました。さらに、精度の高い温度予測データを得られたことで、チームは部品コストや製造アクセシビリティの検討を早めに行い、量産時点で不必要な在庫リスクを最小限に抑えることができました。
シミュレーションの過程で蓄積されたメッシュ設定や境界条件設定、材料特性に関するパラメータは、次世代の製品開発にも流用可能な資産となります。また、結果の可視化によって、どの部品に一番熱ストレスがかかっているか一目瞭然になったため、構造解析チームとも連携して熱応力評価を実行し、筐体素材の厚み変更やネジの配置見直しにつなげられました。
これら一連の作業は、3D CADを中心としたデジタル設計プロセスがあってこそスムーズに実現できたものであり、解析ソフトウェアの機能が充実した現代だからこそ可能なワークフローといえます。何より、開発後期に発覚する不具合を減らして「設計段階での問題点の早期発見と解決」を実現できる点こそが大きな意義です。結果として、製品の信頼性と性能の最適化が図られ、顕在ニーズと潜在ニーズの両方を満たす形でチームの業務効率や技術力向上にも寄与したと総括できます。
熱解析の最新動向と今後の展望
熱解析は今なお進化し続ける領域であり、AI解析やマルチフィジックス解析などの先端技術と融合しながら、新たな可能性を切り開いています。一方で、技術革新のスピードに合わせて設計者が学ぶべき知識やノウハウも増大しており、効率的な情報収集とチーム内でのスキル共有がますます重要になっています。また、通信用デバイスの高速大容量化や自動車の電動化、宇宙開発の加速など、各産業が抱える熱管理の課題はより多様化しており、それだけにシミュレーションの果たす役割も大きくなっています。
AIやマルチフィジックス解析との融合
近年注目を集めているのが、熱解析とAI解析の連携です。これは、過去の膨大な解析結果や実測データを学習させることで、未知のパラメータセットに対しても高速かつ高精度に近い推測が可能となる手法を取り入れるものです。従来は試行錯誤を繰り返しながら最適設計を探していたところを、AIが設計パラメータを提案したり、数値解析の初期条件を自動生成したりすることができるため、設計プロセスの短縮に寄与することが期待されます。
またマルチフィジックス解析においては、熱だけでなく構造、電磁界、音響など複数の物理現象を同時にモデル化し、総合的なシミュレーションを行う取り組みが広がっています。
例えばパワーデバイスの放熱解析では、基板上の電流分布が発熱量に影響を及ぼし、同時に温度上昇がデバイスの抵抗値を変化させる双方向の連成が存在します。AIやマルチフィジックスを駆使すれば、こうした複雑な相関関係を事前に洗い出し、最適な冷却方法や材料選択を一括でシミュレーション可能になるのです。クラウドプラットフォーム上でこれらの仕組みが動けば、高速演算リソースを柔軟に利用でき、大規模モデルでも計算時間を劇的に短縮できます。
最先端のトレンドに敏感なエンジニアたちは、この技術波に乗って、より多面的かつ高度な設計を実現しようとしています。
技術革新がもたらす影響
AIやマルチフィジックス解析の導入が進むことで、設計者の役割は大きく変化しつつあります。従来のように一つひとつ条件を設定して手動で解析を行うだけではなく、解析ソフトウェアや自動化ツールを使いこなし、パラメトリックスタディや最適化アルゴリズムを適切に活用できるエンジニアが求められるようになっているのです。
これにより、統計的手法を用いた信頼性工学の考え方も組み合わせることで、設計段階での不確実性を定量化し、リスク評価を行うことが可能になります。製品開発のスピードアップはもちろん、最終製品の品質向上や開発コストのさらなる削減に直結することが見込まれます。マルチフィジックス解析の活用により、温度による部品変形や振動特性の変化、さらには電気特性の変動など、多面的な因果関係を一度に把握することが可能になり、設計変更の影響範囲を早期に予測できます。
こうした総合力が高まることで、企業や研究機関は競争力のある高品質な製品を迅速に市場投入できるようになり、ひいては産業界全体のイノベーション促進にもつながるでしょう。自動車の電動化や宇宙開発など、今後ますます熱応答の厳しい環境での技術が求められる領域において、熱解析を中心とするシミュレーション技術が新たな変革をもたらす可能性は非常に大きいといえます。
まとめ
ここまで、3D CADを活用した熱解析の重要性と、そのシミュレーション手法について解説してきました。3D CADで作成した正確なジオメトリ情報を使って数値解析を行うことで、製品開発にかかるコストと時間を削減し、品質面でも大きなメリットを得ることができます。
特に、熱伝導・対流・放射の現象を同時に扱えれば、複雑化する現代の製品設計において発生する熱管理上の問題を事前に把握し、設計プロセスの段階で効率的な対策が可能となるのです。さらに、完成した解析モデルをもとに応力解析や流体解析などのマルチフィジックス解析も加えることで、未然の不具合防止や最適化設計を深められます。最新動向として、AI解析や数値シミュレーションの自動化が進んでおり、設計者の作業を大幅に短縮すると同時に、多様な設計案の中から迅速に最適解を引き出すことが可能になりつつあります。
こうした変化は業界全体にも波及し、より高度な技術力と連携体制を備えた組織が市場で優位に立つ時代が到来しているといえます。この知識を活用すれば、競争力のある高品質な製品を早期に市場投入する上で非常に有効な手段となるでしょう。本記事で提示したアプローチを踏まえつつ、自社に適したソフトや手法を組み合わせながら、3D CAD×熱解析を使いこなせる技術力を育成していただければ幸いです。
大手ゼネコンBIM活用事例と 建設業界のDXについてまとめた ホワイトペーパー配布中!
❶大手ゼネコンのBIM活用事例
❷BIMを活かすためのツール紹介
❸DXレポートについて
❹建設業界におけるDX
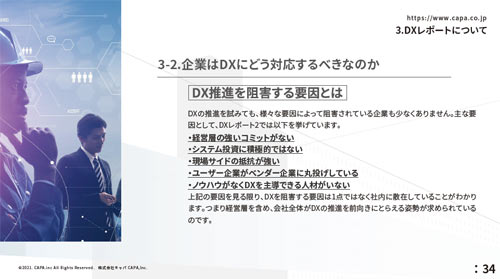
参考情報
・ANSYS公式サイト
https://www.ansys.com/
・COMSOL公式サイト
https://www.comsol.com/
・SimScale公式サイト
https://www.simscale.com/