横河電機のDX推進6ステップと製造業におけるDXの推進事例3選
製造業がDXを進める場合、単に機器を導入してIT化するのではなく現場にある「勘・コツ・ノウハウ」をデジタル化したうえで継承する必要があります。
データを分析活用するスキルや改善意識を持った人材を現場に育成することや、作業や手順勘・コツ・ノウハウを自動化し誰もが使えるように仕組み化することも欠かせません。
この記事では横河電機のDXに対する考え方や横河電機が製造業とともにDXを推進した事例をピックアップしてご紹介します。
横河電機におけるDXとは
横河電機は、DX推進としてビジネスプロセスのオンライン化とサービス化の進展を重視しています。
生産性をより高めるために物理的な制約を受けず、いつでもどこでも社員がオペレーションを回せる状態を目指しているのです。
操業KAIZENソリューションのステップ
横河電機では、モノづくりの現場で DX を実現するための段階として6つのステップを定め、それらをまとめた「操業KAIZENソリューション」を提供しています。(*1)
- ビジョンメイキング・プラン策定
- 計測・制御データの蓄積
- データの紐づけ・意味づけ
- 勘・コツ・ノウハウのデジタル化
- 現場の人材育成
- 仕組化
まずは、製造業の現場ごとにビジョンを描き、現状との差異を明確にしてDXのプランを策定します。
現場の計測器、制御システムなどから取得した情報を蓄積するとともに、データ同士を関連づけたり、情報をまとめたりしてDXに使えるように変換します。
DXの成果が出にくい導入ステップの例
横河電機の分析によると、DXの成果があまり出ていないと感じる場合には、中間のステップを飛ばして以下のような進め方をしているケースが多くみられています。
- ビジョンメイキング・プラン策定
- 計測・制御データの蓄積
- 仕組化
日本のモノづくりは、ベテランや職人などの勘・コツ・ノウハウによって支えられてきました。
そのため、製造業のDXを加速するには、勘・コツ・ノウハウが失われないように工夫する必要があるのです。
横河電機におけるDXの推進事例
製造業では、センサー、コンピューター制御、生産管理などのデバイスやソリューションを導入してデータの取得や分析を重ねます。
原材料の入手可能性や仕掛品の在庫、製造プロセスからリアルタイムデータなどリアルタイムデータを収集して利用し、運用の改善が図れるのです。
ここでは横河電機が自社のDXを推進する際の事例をご紹介します。
定期的なコミュニケーションで共通の目標を立てる
組織は一枚岩が理想ではあるものの、ある組織がサイロ化したり、部門間に分断や隔たりがある状況はやむを得ないといえます。
一方製造業でDXを進めていく場合は、各業務プロセスのインプットとアウトプットに何のデータが必要なのかを詳細に確認しなければなりません。
また、事業全体の戦略とDXの戦略とは十分に連携して同じ目的を掲げて取り組む姿勢も重要です。
そこで横河電機の場合は、部門間での連携を密にするために、DX推進担当のメンバーが、各本部長と少なくとも月に一度は打合せを行っています。
制御・運用技術と情報技術を融合させて顧客に価値を提供する
製造業の場合、工場でラインの仕事を行うため、誰かが工場に行く必要があります。
しかし、現場の人がウェアラブルツールを使えば、工場内の様子が遠隔地からも確認可能です。
顧客理解を高めるために情報部門内でローテーションを行う
情報部門は、インフラの管理やERPの導入・運用といったバックオフィス全般を担っています。
システムの開発はフロントエンドとバックエンドの二つに大別できます。
・フロントエンド:UX、UIなどユーザーが直接触れるWebサービスやアプリケーションの開発担当
・バックエンド:サーバー、データベースなどシステムの安定稼働を維持する担当
DXが進みビジネスプロセスと顧客がエンドツーエンドで繋がることを踏まえると、製造業とはいえCRM(Customer Relationship Management:顧客関係管理)システムやカスタマーポータルの導入が必要です。
顧客やパートナー・関連企業との接点であることも踏まえたシステム構築を行うため、バックエンドとフロントエンドの担当者をローテーションして部門全体の顧客理解向上を図っています。
横河電機の製造業DX支援事例3選
横河電機がDXのコンサルティングとして行った事例をピックアップしてご紹介します。(*2)
製造業のDX事例1:プラント設計・建設のエンジニアリング企業
より厳しい品質管理要件を満たすためにDXを用いてデータと暗黙知の統合に取り組んだ事例です。
課題
・生産設備の老朽化
・ベテラン社員の退職による運用ノウハウの喪失
方法
・ビッグデータ解析/IoTソリューションを導入して、さまざまなソースからデータを取り込み、解析を実施
・生産工程に関するナレッジやノウハウを担当者から聞き取り、高度な分析技術と組み合わせることで根本原因を特定し、工程全体の効率を高める解決策を検討・実施
効果
・オペレーションの安定化による歩留まり向上とコスト削減による、品質と高付加価値なものづくりへの対応力構築
・暗黙知を形式知に変換
・部門間のコミュニケーション改善
・自社内のデータ解析・問題解決スキル向上
製造業のDX事例2:連続プロセス工場
製品品質と生産効率を高めるために、外部データを活用して生産の安定化を図った事例です。
課題
・夜間に生産プロセス変動が起こりやすい
・変動がある場合は、都度オペレーターが調整を実施
・変動の原因は完全に特定されていない
方法
・オペレーターの行動や通常時と変動がある時との稼働状態についてデータを分析して原因を調査
・製造プロセスが変動する原因は、昼夜の周囲温度と大気圧の変動が関連していると特定
・工場内の環境変動を抑えるため、ベテランの工場職員と横河電機の工場職員とで対策を検討し、稼働安定化を図る管理体制を整備
効果
・暗黙知を明示知に変換
・部門間のコミュニケーション改善
・自社内の問題解決能力が向上
製造業のDX事例3:ポリマー生産工場
紙を用いたメンテナンスレポートに含まれる情報を分析し、現場の運用効率と機器の可用性向上を図った事例です。
課題
・紙ベースの点検・巡回報告書が多すぎる
・監督者側は、点検の進捗の把握や対処すべき問題の特定が非常に困難
・点検漏れや過剰整備が発生
方法
・タブレットを導入し、現場の担当者のタスクリストや関連文書などをデジタル化して情報へのアクセス性を改善
・実用化に向け現場担当者、監督者、工場長の意見や今までの保守データなどを分析
・現場作業員や監督者がタブレット画面を介して連携する詳細なワークフローを構築
効果
・メンテナンスコストが10~15%削減
・異常の早期発見による稼働率の向上
・O&M(運用・保守)データの分析・可視化により、生産性向上を図る意思決定支援ツールとして活用
まとめ
横河電機ではDX推進としていかに勘・コツ・ノウハウをデジタル化して意匠伝承を図るかを重視しています。
事例に挙げたように、単にシステムやソリューションの導入だけではなく、現場の担当者や関連メンバー、部門との連携を深めることで製造業のDXがより進められるのです。
大手ゼネコンBIM活用事例と 建設業界のDXについてまとめた ホワイトペーパー配布中!
❶大手ゼネコンのBIM活用事例
❷BIMを活かすためのツール紹介
❸DXレポートについて
❹建設業界におけるDX
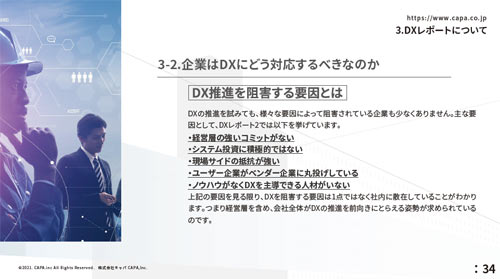
▼キャパの公式Twitter・FacebookではITに関する情報を随時更新しています!
参考URL
*1 https://www.yokogawa.co.jp/solutions/solutions/operational-improvement/
*2 https://www.yokogawa.com/solutions/solutions/digital-transformation/digital-transformation-dx-consulting/