製造業の設計改革を加速!クラウドとデジタルツインで変わるモノづくり
1. はじめに
製造業の現場ではいま、かつてない変化が求められています。多品種小ロットや短納期といった要求の高度化に加え、環境規制への対応や人材不足など、複合的な課題がのしかかっています。これまでのやり方だけでは、もはや競争力を維持することが難しい、そんな時代に突入しています。
こうした環境のなかで、特に見直しが迫られているのが「設計プロセス」です。製品開発の最上流に位置する設計業務は、製品の品質や納期、コストを大きく左右する中核領域。ここを変えることが、製造業全体の変革につながります。
その鍵を握るのが、「クラウドによる設計情報の一元管理」と「デジタルツインによる仮想シミュレーション」の活用です。
クラウド技術を導入すれば、CADデータやBOM情報を安全に集約・共有でき、設計者同士が場所を問わずリアルタイムで協働できる環境が整います。また、デジタルツインでは、現実世界の製品や設備を仮想空間で再現し、実機を使わずに構造や挙動のシミュレーションが可能になります。これにより、試作回数の削減や異常予測の高度化が期待できます。
本記事では、こうした設計DXの全体像を、以下のステップで整理していきます:
- 製造業が現在直面している課題とは何か
- クラウドとデジタルツインがもたらす具体的な効果
- 実際に導入を進めるうえでのステップと成功事例
- 今後の製造業が目指すべきモノづくりの姿
クラウドPDMやデジタルツインは、もはや一部の先進企業だけのものではなく、あらゆる製造業にとっての共通基盤となりつつあります。設計改革をどのように始め、どのように育てていくのか、本記事がそのヒントとなれば幸いです。
2. 製造業における現代の課題と設計プロセスの重要性
製造業がグローバル市場で生き残り、成長を続けていくためには、製造工程だけでなく、より上流にある「設計プロセス」から変革を進める必要があります。多様化する市場ニーズや社会的要請に対応するには、従来のやり方では限界があることが明らかになってきました。
この章では、まず製造業を取り巻く外部環境の変化を整理し、それが設計業務にどのような影響を及ぼしているのかを明らかにします。そして、従来の設計フローではなぜそれらの課題に対応しきれないのか、具体的な限界点を探っていきます。
2.1 グローバル競争と環境規制の影響
第一に、グローバル化が進む中で、製造業はかつてない競争環境にさらされています。新興国を含めた多くの企業が市場に参入し、製品の差別化が難しくなった現在では、短納期・高品質・低コストの三拍子をいかに成立させるかが、企業の競争力を左右する重要なポイントとなっています。
こうした中で、製品のライフサイクルは年々短縮され、需要はますます多様化し、少量多品種生産が当たり前になりつつあります。その結果、どれだけ迅速に、かつ確実に製造条件や仕様変更へ対応できるかが、事業の成否を分ける分岐点になっています。
第二に、地球環境問題への関心の高まりや、持続可能な開発目標(SDGs)の普及に伴い、環境規制が年々厳格化しています。これにより、設計段階から「廃棄」「再利用」「リサイクル」など、製品のライフサイクル全体を視野に入れた取り組みが求められるようになりました。環境配慮型の製品設計ができなければ、国際競争力を失うだけでなく、企業の社会的評価やブランド価値にまで悪影響が及ぶリスクがあります。
さらに深刻なのが、技術人材の不足です。熟練技術者の高齢化とともに、若手設計者の確保や育成が追いつかない現状が多くの企業で課題となっています。属人化した設計ノウハウの継承が困難になる中で、業務の標準化や設計プロセスの可視化、そしてデータの一元管理といった仕組みが急務となっています。
このように、外的要因(市場環境・規制)と内的要因(人材・情報管理)が複雑に絡み合いながら、設計部門にはこれまで以上に柔軟でスピーディな対応が求められています。これらの課題に対する根本的な解決策として、設計プロセスそのものの構造改革、すなわち設計DXへの取り組みが期待されています。その中核となるのが、クラウドとデジタルツインです。
2.2 従来の設計プロセスの限界
従来の設計現場では、CAD図面やBOM(部品表)などの情報が部門ごと・拠点ごとに分散して管理されているケースが多く、業務間の連携が滞りやすい状態にありました。設計や仕様変更に関する情報共有がメールや紙ベースで行われると、最新情報の行き違いや確認漏れが発生し、プロジェクト全体の進行に影響を及ぼします。
また、設計段階で構造や挙動のシミュレーションを行う際にも、専用ソフトがローカル環境に限られているため、使用できる計算リソースが不足しがちです。加えて、ソフトウェアのライセンス数や操作スキルの制約から、実務に十分活かしきれない状況が発生しています。その結果、実機による試作を繰り返す必要が生じ、開発コストの増加やリードタイムの長期化につながっていました。
さらに、設計変更の影響が十分に社内で共有されないまま製造に入ると、不具合や仕様ミスマッチが発生するリスクも高まります。設計部門と製造現場の連携が不十分なままだと、問題の発見が遅れ、後戻りややり直しが頻発する原因にもなります。
このような課題の根本には、「情報が分断されていること」と「判断が属人的であること」があります。業務の標準化やデータの一元化が進まない限り、設計プロセスの効率化も高度化も期待できません。
しかし、ここにクラウド技術を導入することで、設計情報の共有と管理を飛躍的に改善できる可能性が生まれます。また、デジタルツインを活用すれば、実機を用いずにシミュレーションを重ねながら最適設計を追求することも可能になります。こうした「設計DX」の取り組みが、従来の限界を突破し、新たな製造価値の創出につながっていくのです。
3. クラウド技術の導入とそのメリット
設計改革の起点として、近年急速に注目を集めているのが「クラウド技術」の活用です。これまでオンプレミスで個別に管理されてきた設計データを、クラウド上で一元的に管理・共有できるようになることで、設計現場に多くの変化がもたらされています。
特に、CAD図面やBOM(部品表)などの製品データを管理する「クラウドPDM(製品データ管理)」や、製品ライフサイクル全体を見渡して管理する「クラウドPLM(製品ライフサイクル管理)」は、設計DXを支える基盤技術として定着しつつあります。
ここでは、これらのクラウド型管理システムがもたらすメリットと導入効果について、具体的に見ていきます。
3.1 クラウドPDM/PLMの概要と利点
クラウドPDMやPLMとは、従来のようにローカルサーバや各部門ごとのPCに分散していた設計情報を、クラウド上のプラットフォームで一元管理する仕組みです。PDM(Product Data Management)は、主にCADデータや図面、部品構成表(BOM)などを整理・保管・追跡する役割を持ち、PLM(Product Lifecycle Management)は、それらに加えて製品企画から廃棄に至るまでの情報を横断的に扱う、より広範な管理機能を備えたシステムです。
クラウド型の最大の特長は、導入・運用コストを柔軟に調整できる点にあります。オンプレミスの場合は、サーバの構築・保守やライセンス契約などに多額の初期投資が必要でしたが、クラウド型ではサブスクリプション方式が一般的で、必要なときに必要な分だけ使える仕組みになっています。これにより、事業規模や導入フェーズに応じてスモールスタートしやすくなりました。
また、クラウド上のデータはインターネット経由でアクセスできるため、遠隔地の拠点や外注先ともリアルタイムで同じ情報を共有できます。設計者、調達担当者、製造現場などがそれぞれの立場から同じデータを確認しながら業務を進められるようになり、情報の行き違いや重複作業といった非効率を大幅に削減できます。
一方で、情報の安全性も重要な要素です。クラウド型では、ユーザーごとのアクセス権限やログ管理、暗号化通信などを活用することで、企業の機密情報を保護する仕組みが整っています。権限設定を適切に行えば、設計者は書き込みができるが製造部門は閲覧のみ、といった柔軟な運用が可能です。
このように、クラウドPDMやPLMは、コスト削減と情報共有の効率化を同時に実現できる現実的なソリューションとして、多くの製造業で導入が進んでいます。
3.2 クラウドによるデータの一元管理とアクセス向上
クラウドを活用すれば、これまで分散していたCADデータや図面、製造指示書などを1つの環境に集約して保管できます。これにより、社内の誰もが必要なときに、常に最新版のデータへ迅速にアクセスできるようになります。多くのクラウドPDM/PLMには、自動バージョン管理や変更履歴の追跡機能が備わっており、更新ごとの差分や過去の状態を簡単に確認できるため、改版ミスのリスクを抑えることができます。
また、複数の部門や拠点が1つのクラウド基盤を利用することで、情報の流れがシンプルかつ透明になります。従来よくあった「最新版を取り違えてしまった」「更新された情報を知らずに作業を進めてしまった」といったトラブルが減り、業務全体の信頼性が高まります。
この情報一元化のメリットは、デジタルツインとの連携においても顕著です。たとえば、実際の製造装置や運用中の設備から取得したIoTセンサーデータをクラウドに集約し、そこから設計段階のシミュレーションモデルに反映させることで、リアルタイムな評価と改善が可能になります。物理世界で起こっている現象が即座に仮想世界へ反映される仕組みが整えば、開発スピードも精度も飛躍的に向上します。
特に、多頻度の設計変更が発生する現場では、クラウドによる情報共有の即時性が非常に大きな武器となります。たとえば、営業から顧客要望の変更が伝えられた場合でも、その内容がすぐに設計部門や製造部門に共有され、全体で対応方針を決定できます。このようなスピード感のある情報伝達と意思決定は、競争環境が激しい製造業において重要な差別化要因となるのです。
3.3 リモート協働の強化とプロジェクト管理の効率化
クラウド技術のもうひとつの大きな強みは、リモート環境における柔軟な設計体制を実現できる点です。グローバルに展開する企業では、設計者や技術者が拠点ごとに分散していることが多く、また昨今の人材不足を背景に、外部パートナーやフリーランスの技術者を積極的に活用する動きも広がっています。こうした分散したチームでも、クラウドベースの設計環境を整えれば、同じプロジェクトデータを参照・編集しながら業務を進めることができます。
たとえば、ある設計者がCAD図面を更新すれば、その変更は即座に他部門や協力会社にも共有され、フィードバックや修正指示がその場で行われます。従来は数日かかっていた情報確認や調整作業が、リアルタイムで完結するようになり、プロジェクト全体のスピードと柔軟性が向上します。
さらに、クラウド環境では、設計データだけでなく進捗管理や課題管理の機能も統合することができます。設計DXの取り組みにおいては、まず小規模なPoC(概念実証)から始めて、成果を測定しながらスケールアップしていくアプローチが主流です。この過程で、マイルストーンやKPI、作業担当の見える化がクラウド上で行えると、プロジェクトの透明性と説明責任が大きく向上します。
また、クラウドを活用したプロジェクト運営は、物理的な制約に縛られないため、人的リソースの最適配置にも貢献します。設計スキルや専門性をもとに、チーム編成や作業分担を柔軟に調整できるようになることで、少人数でも最大限の成果を引き出す組織運営が可能となります。結果として、期間短縮・コスト削減・品質安定といった複数の成果を同時に得ることができるのです。
4. デジタルツインの活用と設計革新
製造業における「デジタルツイン」は、単なる仮想モデルではありません。現実の製品や設備とリアルタイムで連動するデジタルな“もう一つの存在”として、設計や開発、運用における判断精度やスピードを大きく引き上げる可能性を秘めています。
とりわけ設計の現場では、デジタルツインを活用することで、これまで試作や実機テストに頼っていた工程の一部を、仮想空間上でのシミュレーションに置き換えることが可能となります。これにより、コストの削減だけでなく、設計の自由度や精度も大きく向上します。
この章では、まずデジタルツインの基本概念と設計現場への応用方法を整理したうえで、試作削減やリアルタイムデータ活用による品質改善など、実務面での活用ポイントを解説していきます。
4.1 デジタルツインの基本と設計への応用
デジタルツインとは、現実の製品や設備を仮想空間に再現し、実際の動作や状態をリアルタイムで反映し続けることで、あたかも現実と“対になる存在”のように連携して機能する仕組みです。これにより、製品の構造や挙動を仮想上で何度でもシミュレーションでき、従来であれば試作や実機評価に頼っていた作業を事前に検証することが可能となります。
設計への応用としては、まず3D CADで作成したモデルをベースに、運用時の温度、圧力、振動など、現実の使用環境を仮想空間に再現します。そのうえで、荷重や応力といった物理条件を与えてシミュレーションを行うことで、形状や材質の選定による性能変化を評価できます。これにより、設計者は早期の段階で最適化の方向性を掴むことができ、後工程での仕様変更や手戻りのリスクを抑えられます。
また、デジタルツインは単なるモデル検証にとどまらず、設計判断の質を高めるツールとしても有効です。たとえば、異常予兆を検知するアルゴリズムをモデルに組み込むことで、特定の条件下での振動増加や温度上昇といった異常傾向を、事前に可視化できます。実機から得られるセンサーデータとリンクさせることで、シミュレーションはより現実的なものとなり、判断の精度を飛躍的に向上させるのです。
このように、デジタルツインを設計の初期段階に取り入れることで、設計品質の向上はもちろん、開発スピードの加速やコスト削減といった多方面での効果が期待できます。今や、設計プロセスにおける“第三の目”として、デジタルツインの価値は確実に高まりつつあります。
4.2 シミュレーションによる試作コストの削減
実際のモノづくりにおいて、試作品の作成には大きな負担が伴います。材料費や加工コストだけでなく、試作・検証に関わる人員の確保やスケジュール調整も必要になり、特に多品種小ロット生産では、試作工程がボトルネックとなることが少なくありません。
デジタルツインを活用すれば、これらの物理試作の一部を仮想空間で置き換えることができます。例えば、形状変更による応力分布の変化、特定の荷重条件下での振動や変形の程度など、物理現象を高精度で再現したシミュレーションにより、設計上の懸念点を早期に洗い出すことが可能です。
また、設計案を何パターンも比較検討したい場面でも、実機試作では時間とコストの制約が付きまといますが、デジタル環境であればそのハードルは大きく下がります。何度でも条件を変えてテストできる柔軟性があるため、アイデアを検証するスピードも飛躍的に上がります。設計者はより多くの選択肢を検討でき、完成度の高い製品設計を目指しやすくなるのです。
もちろん、すべての試作が不要になるわけではありませんが、最もコストのかかる初期試作の回数を減らすことで、製品開発全体のスピードアップとコスト圧縮を両立できる点は非常に大きなメリットです。特に競争が激しい製品分野では、こうした“試作の仮想化”による迅速な商品化が、企業の市場優位性に直結します。
4.3 リアルタイムデータとの連携による品質向上
デジタルツインの魅力は、設計段階だけでなく、製造・運用・保守といった下流工程においても活用できる点にあります。特に、リアルタイムに取得した実機の稼働データを仮想モデルに反映させることで、運用中の状態変化をシミュレーション環境でも“追体験”できるようになります。
たとえば、工場内の設備が通常より高い負荷で稼働している際、どの部品が先に劣化しやすいのか、どの条件下で異常が発生しやすいのかを、リアルタイムでモデル上に再現できます。これにより、保守設計の段階であらかじめ予測された故障モードに応じて、交換部品の確保やメンテナンススケジュールの最適化が行えるようになります。結果として、計画外の稼働停止や修理コストの抑制が可能となるのです。
また、こうした運用中のデータは、次期製品の設計にもフィードバックできます。実環境での使用状況に基づく設計改善が繰り返されることで、製品全体の信頼性とユーザビリティが継続的に向上していきます。つまり、デジタルツインは単なる“シミュレーター”ではなく、企業の製品ライフサイクル全体にわたる「改善ループ」を支える基盤として機能するのです。
このように、リアルとバーチャルを往復する情報の流れを確立することで、設計から運用・保守、そして再設計へとつながる持続的な品質向上のサイクルが生まれます。そしてその中心にあるのが、クラウドと連携したデジタルツインなのです。
5. 実践的な導入ステップと実践シナリオ
クラウドやデジタルツインの有効性は理解できても、「実際にどう導入すればよいのか」「本当に自社でも成果が出せるのか」といった不安を持つ企業も少なくありません。特に、ITインフラが整っていない中小企業や、レガシーシステムが残る現場では、全社的な導入を一気に進めることが難しいのが実情です。
そこで本章では、導入を現実的かつ着実に進めていくための「段階的アプローチ」と、実際にクラウドとデジタルツインを導入して成果をあげた企業の事例を紹介します。最初から完璧を目指すのではなく、小さな成功を積み重ねていくことが、設計DXの定着とスケール拡大につながります。
5.1 段階的な導入と評価の重要性
クラウドPDMやデジタルツインといった先進的な技術は、大きな可能性を持つ一方で、導入そのものが目的化してしまうと、現場に混乱を招くおそれもあります。そこで有効なのが、小規模な導入から始める「スモールスタート」の考え方です。いきなり全社で使おうとせず、まずは1つの製品ラインやプロジェクトに限定して導入し、その効果を丁寧に検証することが、成功への近道になります。
この段階では、評価指標(KPI)を事前に明確に定めておくことが重要です。たとえば「設計変更に伴う手戻り件数の減少」「試作回数の削減率」「設計から製造までのリードタイム短縮」など、定量的な数値で成果を測ることで、社内の理解や納得感も得やすくなります。定性的な「なんとなく便利になった」という印象では、他部署の協力や経営層の意思決定を引き出すには不十分です。
また、既存の業務システムとの共存を意識することも不可欠です。すでに社内にあるCADソフトやファイルサーバ、オンプレミスのPDM環境と新しいクラウドツールをどう連携させるか。セキュリティポリシーに照らして、どの範囲までクラウド化を進めるか。こうした実務的な検討を並行して行うことが、現場の混乱を最小限に抑えるポイントです。
段階的に導入し、効果を確認しながら展開範囲を広げていくことで、リスクを抑えつつクラウドとデジタルツインを業務に定着させることができます。大切なのは、導入の成否を「システムが動いたかどうか」ではなく、「業務にどのような変化が起きたか」という視点で評価することです。その意識が、設計DXを単なる技術導入ではなく、組織的な価値創出へと昇華させる鍵となります。
5.2 実践シナリオとその学び
ここでは、クラウドPDMやデジタルツインを段階的に導入した場合の「想定シナリオ」を紹介します。これは実在の企業事例ではありませんが、製造業の設計改革を進める際に想定される現実的な展開モデルとして、多くの現場に応用できる要素を含んでいます。
【モデル企業の背景】
たとえば、従業員300名規模の機械装置メーカーを想定してみましょう。従来は設計情報を部門ごとにローカルで管理しており、設計変更の共有がメールや口頭に頼っていたため、手戻りや調達ミスが頻発していました。外部サプライヤーとの図面のやり取りにも時間がかかり、設計から製造までの一連の流れに多くのムダが生じていたのです。
【クラウドPDM導入フェーズ】
この企業が最初に着手したのは、クラウドPDMの導入でした。全社員が常に最新版のCAD図面や部品表(BOM)にアクセスできる仕組みを整えたことで、設計変更の反映が迅速になり、製造現場や調達部門との連携ミスが大幅に削減されました。さらに、サプライヤーにも限定的にクラウド環境を開放し、共通プラットフォーム上で図面や仕様を共有することで、調達のスピードと精度も向上しました。
【デジタルツイン導入フェーズ】
続いて、クラウド環境の整備が進んだ段階で、構造シミュレーションを活用した「設計デジタルツイン」の導入に踏み切りました。運用時の負荷を想定した仮想モデルを設計時点で構築し、CAD上で事前検証を繰り返すことで、物理的な試作を従来の半数以下に抑えることができたという想定です。結果として、開発にかかる期間を短縮しつつ、製品完成度を高め、市場投入までのスピードを大きく向上させることが可能になりました。
【シナリオからの学び】
このようなモデルケースから学べるのは、「段階的な導入」と「定量評価の徹底」が成功の鍵であるという点です。クラウドPDMで設計情報の整流化に取り組み、そこで得られた改善効果をベースにデジタルツインを導入することで、無理なく設計DXをスケールアップさせています。
また、PoC(概念実証)による導入初期の成果を数値で見える化し、関係部署と共有することで、社内の協力体制や次フェーズへの予算確保もスムーズに進めやすくなります。技術だけでなく、業務プロセスや組織文化を含めて変えていく「全体最適」の視点が、DXを成功させる大きな要因といえるでしょう。
さらに、こうした実践的な取り組みを経営層が主導することで、設計DXは単なるシステム導入ではなく、企業戦略の中核として根づいていきます。経営判断と現場改善が一体となった変革こそが、持続可能な競争力につながっていくのです。
6. クラウドとデジタルツインがもたらす未来のモノづくり
クラウド技術とデジタルツインは、単なる業務効率化のツールではなく、製造業のビジネスモデルそのものを大きく変える可能性を秘めています。これらの技術を設計プロセスに導入することで、コスト削減や納期短縮といった直接的な成果だけでなく、事業の柔軟性や将来性にまで広がる波及効果が期待できます。
今後、設計と製造をつなぐ情報の流れがますますリアルタイム化・高度化していく中で、クラウドとデジタルツインは「新しいモノづくりの当たり前」として定着していくでしょう。この章では、これらの技術が生み出す新たなビジネスモデルや、技術革新による競争力の強化といった未来展望について考察します。
6.1 新たなビジネスモデルと持続可能性
これまでの製造業では、製品を設計し、作って売るという“モノの販売”が基本的なビジネスモデルでした。しかし今では、クラウドやデジタルツインを活用することで、製品そのものを「サービス」として提供する“サービタイゼーション”という考え方が急速に浸透し始めています。
たとえば、クラウド基盤とデジタルツインを組み合わせれば、製品がどのように使われているのかをリアルタイムで把握することができます。それにより、故障が起きる前にメンテナンスを提供したり、最適な運用方法をアドバイスしたりと、顧客と長期的な関係性を築くことが可能になります。これまで「納品したら終わり」だったビジネスは、サービス提供を通じて継続的に価値を提供するモデルへと進化していくのです。
また、デジタルツインを活用すれば、製品のライフサイクル全体を通じた最適化も現実のものとなります。部品の再利用性や、廃棄時のリサイクル設計を事前に考慮することで、環境に配慮したモノづくりが可能になります。設計段階で環境負荷を数値化し、製品ごとの環境スコアを可視化する取り組みも広がっており、これらはSDGsへの貢献だけでなく、企業のブランド価値を高める重要な要素にもなっています。
こうした環境配慮型設計や製品のサービス化といったアプローチは、特に海外市場での競争において強い差別化要因となります。グローバル展開を視野に入れる日本の製造業にとって、クラウドとデジタルツインを活用したサステナブルかつサービス指向のモノづくりは、これからの国際競争に勝ち抜くうえで欠かせない戦略といえるでしょう。
つまり、これらの技術がもたらすのは単なる作業の効率化ではなく、「価値の提供方法そのもの」を再定義する大きな転換です。製造業は今、プロダクトアウトからマーケットイン、そして「アウトカム志向」へと進化しようとしています。その中核を支えるのが、クラウドとデジタルツインという新しい設計基盤なのです。
6.2 技術革新による競争力の強化
クラウドとデジタルツインを起点に設計DXを進めることで、企業はさまざまな技術革新に対応しやすい柔軟な体制を手に入れることができます。これにより、新たな技術やサービスを積極的に取り込み、製品開発やビジネスのスピードを加速させる「変化への即応力」が強化されていきます。
たとえば、今後さらに注目されるのが、AIによる設計支援の高度化です。クラウド環境に蓄積された過去の設計データやシミュレーション結果をもとに、AIが最適な設計案を提案するといった取り組みも進みつつあります。これにより、設計者はより複雑で創造性の高い課題に集中できるようになり、製品の差別化につながる部分に力を注ぎやすくなります。
さらに、デジタルツインと生産システムが連携することで、製造工程そのものの仮想検証も可能になります。たとえば、生産ラインのレイアウト変更やロボットの動作計画を仮想空間上で検証し、不具合のリスクを最小化したうえで実機に反映する手法はすでに一部の企業で実践され始めています。これにより、立ち上げ期間の短縮やトラブル回避が実現でき、製造現場の生産性と安定性が同時に向上します。
加えて、クラウドを介して外部パートナーや研究機関とも設計情報を共有することで、オープンイノベーションも促進されます。国内外の大学、ベンチャー企業、顧客企業といった多様な関係者と協働しながら、新しい素材や技術、製品アイデアをスピーディに形にしていく体制を築くことが可能になります。
このように、クラウドとデジタルツインを軸とした設計基盤は、単なる社内業務の効率化にとどまらず、技術革新を呼び込む土壌としても機能します。企業が未来に向けて競争力を高めるためには、こうした「変化をチャンスに変える力」を持った設計体制づくりが、これからますます重要になっていくのです。
7. おわりに
製造業における設計業務は、かつてない変化の波にさらされています。多様化する市場のニーズ、短納期化、環境への配慮、そして人材不足——これらの課題を乗り越えるために、設計のあり方そのものを見直す必要がある今、クラウドとデジタルツインの活用は単なる選択肢ではなく、次の時代への前提条件になりつつあります。
クラウドPDMによる設計データの一元管理や、リアルタイムでのコラボレーション環境の整備は、情報共有の質とスピードを大きく高め、組織全体の連携力を底上げします。そして、デジタルツインの導入によって、試作や評価のプロセスは仮想空間へと移り、設計者はより早く・より確かな意思決定を下すことが可能になります。これにより、開発の自由度と精度が同時に高まり、製品の価値そのものを高めることができるのです。
しかし、こうした技術導入はゴールではありません。重要なのは、これらの技術を“使える状態”にすること、そして“継続的に活かし続けられる組織”へと育てていくことです。PoC(概念実証)による小さな一歩を積み重ね、効果を可視化し、現場に定着させることで、やがてそれは企業全体を巻き込む変革へと広がっていきます。
設計DXは、単なるツール導入ではなく、「組織の設計力を最大限に引き出すための進化」です。クラウドとデジタルツインがもたらすのは、技術的な効率化にとどまらず、価値創造のあり方そのものを再定義する力でもあります。
変化の激しい時代において、柔軟に新技術を取り入れ、設計者がより深い判断を下せる環境を整えること。
それこそが、これからの製造業が持続的に成長するための礎となるでしょう。
建築・土木業向け BIM/CIMの導入方法から活用までがトータルで理解できる ホワイトペーパー配布中!
❶BIM/CIMの概要と重要性
❷BIM/CIM導入までの流れ
❸BIM/CIM導入でよくある失敗と課題
❹BIM活用を進めるためのポイント
についてまとめたホワイトペーパーを配布中
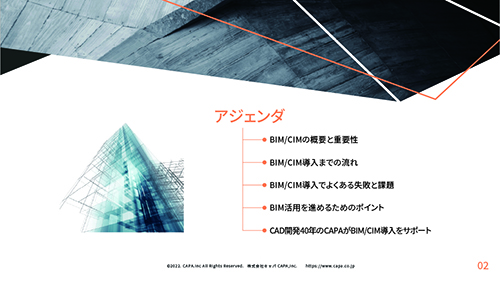
参考情報
・2024年版ものづくり白書(ものづくり基盤技術振興基本法第8条に基づく年次報告) (METI/経済産業省)
https://www.meti.go.jp/report/whitepaper/mono/2024/index.html
・PDM とは | 製品データ管理 | Autodesk
https://www.autodesk.com/jp/solutions/pdm-product-data-management
・3DEXPERIENCEプラットフォーム